In the world of manufacturing, especially in industries dealing with tube production, the efficiency and quality of the products rely heavily on the design and maintenance of the machinery involved. One critical component that plays a significant role in this is the mould used within tube mills. Replacement moulds for tube mills have emerged as an essential aspect of maintaining production standards, reducing downtime, and ensuring the longevity of manufacturing equipment.
**What Are Tube Mills and Their Importance?**
Tube mills are essential machines in the manufacturing process used to create various types of pipes and tubes for numerous applications, from construction to automotive and beyond. These mills can produce tubes in various shapes and sizes, making them versatile tools for manufacturers. The efficiency of a tube mill is largely dependent on its design, including the use of moulds that shape the semi-finished material into the finished product.
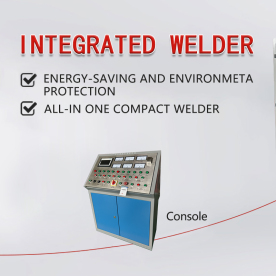
Understanding Replacement Moulds for Tube Mills: Enhancing Efficiency and Reducing Downtime in Manufacturing Processes
**The Role of Replacement Moulds**
Moulds in tube mills form the key shaping element that dictates the final dimensions and tolerances of the production. Replacement moulds are crucial when the existing moulds wear out or when the manufacturer decides to produce a different product. These replacement moulds need to be of high quality, designed to fit the specific dimensions of the machines, and made from durable materials to withstand the stresses of the manufacturing process.
**Why Consider Replacement Moulds?**
1. **Improved Product Quality**: Over time, the moulds wear down, leading to inconsistencies and defects in the finished products. Replacement moulds can ensure that the final products meet the required specifications, contributing to improved overall quality.
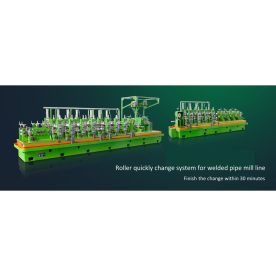
Understanding Replacement Moulds for Tube Mills: Enhancing Efficiency and Reducing Downtime in Manufacturing Processes
2. **Minimized Downtime**: Manufacturing downtime can be extremely costly. Having readily available replacement moulds means that production lines can be swiftly restarted, reducing lost production time due to maintenance or unexpected breakdowns.
3. **Cost-Effectiveness**: While the initial investment in high-quality replacement moulds can be significant, they often lead to lower operational costs over time. Superior moulds offer enhanced durability, decreasing the frequency of replacements and repairs needed.
4. **Adaptability to Market Needs**: Market demands can shift, and being able to quickly switch to different moulds allows manufacturers to adapt to new production requirements without significant delays.
5. **Enhanced Performance and Productivity**: With fresh, precise moulds in place, tube mills operate more efficiently, resulting in increased production rates and lowering the cost per unit.
**Choosing the Right Replacement Moulds**

Understanding Replacement Moulds for Tube Mills: Enhancing Efficiency and Reducing Downtime in Manufacturing Processes
Selecting the right replacement moulds is critical for maintaining optimal tube mill performance. Here are some key factors to consider:
– **Compatibility**: The replacement moulds must fit the existing machines precisely. This requires detailed measurements and potentially consulting the machine’s specifications. – **Material Quality**: The materials used in the moulds should be robust enough to withstand high pressures and temperatures, which are common in production processes. Stainless steel and high-speed steel are popular choices due to their durability.
– **Design Precision**: The design of the moulds should reflect the technical requirements of the products being manufactured. Precision in design translates to accuracy in the finished product, reducing waste and ensuring higher quality.
– **Supplier Reliability**: Working with trustworthy suppliers who specialize in replacement moulds for tube mills is essential. They can also offer insights into the latest technologies and materials that can enhance mould performance.
**Conclusion**
The importance of replacement moulds for tube mills cannot be overstated. They are not merely components; they are integral to the quality, efficiency, and productivity of tube manufacturing processes. By investing in high-quality replacement moulds and choosing the right suppliers, manufacturers can ensure their operations run smoothly and adapt to the ever-changing market demands. As with any piece of machinery, regular maintenance and the timely replacement of moulds will lead to long-term success in the manufacturing sector.Cost-Effective Spare Parts for Tube Mills