Metal 3D printing is already a multi-billion-dollar global industry. The additive manufacturing approach is poised to disrupt many facets of construction and will only continue to grow for the foreseeable future. The technology isn’t homogenous, however. Much like plastic printing, there are several different approaches, each with their own pluses and minuses.
A new method announced this week by a team at MIT prioritizes printing speeds and scale (object size) over resolution. As outlined, the system is capable of printing large aluminum parts “at least 10 times faster than a comparable metal additive manufacturing process.”
Liquid metal printing (LMP) utilizes a bed of 100-micron glass beads to create a structure into which molten aluminum is deposited — a process not entirely dissimilar from injection molding. The beads are capable of standing up to the intense temperature, while allowing the heat to quickly dissipate as the metal solidifies.
Given that aluminum is classified as an “infinitely recyclable” material, the team behind the work envisions pairing this system with a machine that melts the metal into molten form. Such a combination could prove invaluable for construction sites, bringing faster speeds and larger objects at a lower cost.
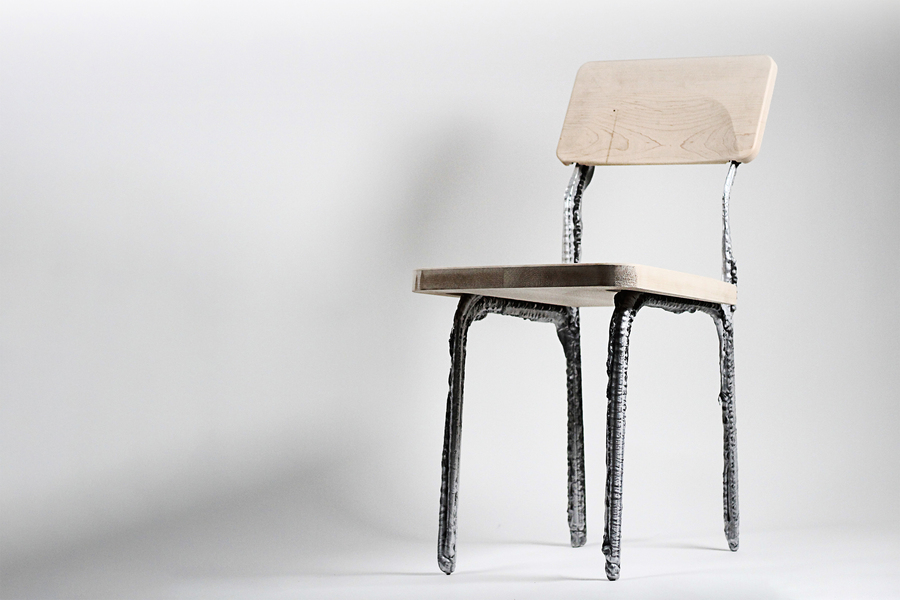
There is, however, at least one big caveat: resolution. As evidenced in the images, the final product doesn’t offer near the pinpoint accuracy of some other methods. The resulting metal objects are bumpy and uneven, resembling the product of fused deposit modeling (FDM), which extrudes plastic layer by layer. Aluminum can, of course, be sanded down, though that’s likely additional time and money most won’t want to introduce into the process.
“The liquid metal printing really walks the line in terms of ability to produce metal parts in custom geometries while maintaining quick turnaround that you don’t normally get in other printing or forming technologies,” says Jaye Buchbinder of Emeco, a furniture company that helped fund the study. “There is definitely potential for the technology to revolutionize the way metal printing and metal forming are currently handled.”