**Introduction**
In the world of metal forming and manufacturing, tube mills play a crucial role in the production of tubular products. These machines, designed to create seamless tubes and pipes from flat metal sheets, rely heavily on the performance and functionality of various components. Among these, the rollers of a tube mill stand out as key elements that significantly influence the quality, efficiency, and speed of the manufacturing process. This article explores the importance of rollers in tube mill operations, the different types of rollers used, and how to optimize their performance for enhanced production outcomes.
**The Importance of Rollers in Tube Mills**
Rollers in tube mills perform several critical functions that are essential for the effective production of high-quality tubular products. Their primary roles include:
1. **Forming and Shaping**: Rollers are responsible for forming flat metal strips into cylindrical shapes. This initial phase is pivotal as it dictates the final dimensions, roundness, and structural integrity of the tubes produced.
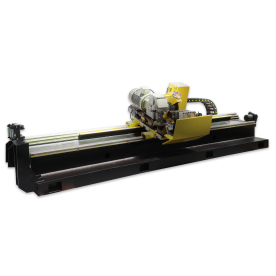
Understanding the Role of Rollers in Tube Mill Operations: A Comprehensive Guide for Manufacturers and Engineers
2. **Welding Preparation**: In many tube mill configurations, rollers help prepare the edges of the metal strips for welding. Precise alignment and shaping ensure optimal contact and a robust weld, which is crucial for the durability of the finished product.
3. **Finishing and Sizing**: After the initial formation, additional sets of rollers help in sizing and scaling the tubes to their final dimensions. This finishing process can affect the wall thickness and overall surface quality of the pipes.
4. **Guidance and Support**: Rollers also aid in guiding the metal strip through the mill, ensuring that it maintains a consistent path throughout the forming and welding processes.
**Types of Rollers Used in Tube Mills**
A variety of roller types are employed in tube mills, each designed for specific functions and to accommodate different materials and thicknesses. Common types of rollers include:
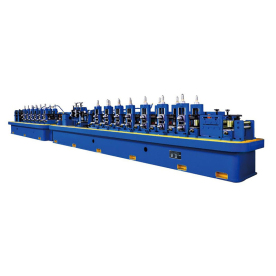
Understanding the Role of Rollers in Tube Mill Operations: A Comprehensive Guide for Manufacturers and Engineers
1. **Forming Rollers**: These are among the first rollers encountered in the tube mill process. They shape the flat strip into a cylindrical form through a sequence of passes.
2. **Welding Rollers**: Positioned where the edges of the strip are joined, welding rollers help align and support the weld seam, ensuring that the welding process is efficient and produces a strong bond.
3. **Sizing Rollers**: After welding, sizing rollers refine the final tube dimensions. These rollers ensure that the product meets strict tolerances and specifications before entering the subsequent finishing stages.
4. **Finishing Rollers**: Used for surface treatment and enhancement, finishing rollers improve the surface quality of the tube, removing any imperfections and preparing it for further processing or coating.
**Optimizing Roller Performance**
In order to maximize the efficiency and effectiveness of tube mills, manufacturers and engineers must focus on optimizing roller performance. Several strategies can be employed:

Understanding the Role of Rollers in Tube Mill Operations: A Comprehensive Guide for Manufacturers and Engineers
1. **Material Selection**: Choosing the right material for rollers is critical. High-quality alloys and hardening techniques can significantly improve the wear resistance and longevity of rollers, reducing downtime for replacements and maintenance.
2. **Precision Engineering**: Ensuring that rollers are accurately machined and aligned is vital. Deviations in roller geometry can lead to inconsistent product quality, increased scrap rates, and ultimately, higher production costs.
3. **Regular Maintenance**: Implementing a regular maintenance schedule helps prevent wear and tear on rollers. This includes consistent lubrication, inspection for signs of damage, and replacement when necessary.
4. **Technological Integration**: Utilizing advanced technology such as automation and real-time monitoring systems can help optimize roller settings and configurations, ensuring that adjustments can be made quickly to maintain optimal performance levels.
**Conclusion**
Rollers play an indispensable role in the operation of tube mills, heavily influencing the production process and the quality of the end products. Understanding the various functions of these rollers, the types available, and strategies for optimization is essential for manufacturers seeking to improve their tube mill operations. By focusing on these aspects, businesses can not only enhance their production capabilities but also ensure that they remain competitive in the ever-evolving landscape of the manufacturing industry.Automatic Pipe making machine