****
In today’s fast-paced industrial landscape, manufacturers are continually seeking ways to optimize their production processes, enhance efficiency, and reduce costs while maintaining high-quality standards. A Scalable Pipe Mill Production Line System has emerged as a vital component in achieving these objectives, enabling companies to adapt to varying market demands and streamline operations. This article explores the significance, components, benefits, and implementation of scalable pipe mill production line systems in the context of modern manufacturing.
What is a Scalable Pipe Mill Production Line System?
A Scalable Pipe Mill Production Line System refers to a manufacturing setup designed specifically for the production of pipes, which can be adjusted in scale according to the production requirements. These systems are integrated with advanced technologies and modular components that allow manufacturers to easily increase or decrease their output without significant downtime or capital investment. The adaptability of these systems is crucial for industries dealing with fluctuating demand or diverse product lines.
Key Components of a Scalable Pipe Mill Production Line
1. **Modular Machinery**: At the heart of a scalable production line are modular machines that can be configured or reconfigured to accommodate different pipe sizes, materials, and production rates. This modularity facilitates easy upgrades and maintenance.
2. **Automated Systems**: Incorporating automation in the production line enhances productivity and precision. Robotics can be employed for material handling, cutting, welding, and even quality inspection, significantly reducing human errors and labor costs.
3. **Quality Control Systems**: Advanced quality control mechanisms, including inline inspection systems, ensure that every pipe produced meets strict industry standards. This not only reduces waste but also enhances customer satisfaction.
4. **Data Integration**: Modern scalable pipe mill systems are equipped with Industry 4.0 technologies such as IoT sensors and data analytics platforms. This integration allows for real-time monitoring of the production process, offering insights that lead to better decision-making and operational efficiencies.
Benefits of Scalable Pipe Mill Production Line Systems
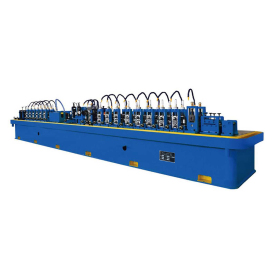
Understanding the Scalable Pipe Mill Production Line System: Enhancements in Efficiency, Flexibility, and Productivity for Modern Manufacturing
1. **Efficiency and Cost-Effectiveness**: One of the primary benefits of scalable systems is their ability to optimize production efficiency. By adjusting the scale of operations based on demand, manufacturers can minimize idle time and reduce operational costs. The result is a leaner operation that maximizes output per resource spent.
2. **Flexibility**: Manufacturers can quickly adapt to changing market conditions or customer requirements. The ability to switch between different pipe specifications or sizes within the same production line allows for increased flexibility and capability to respond to trends.
3. **Improved Product Quality**: With integrated quality control systems, companies can ensure consistent quality across all products. Automated systems reduce the risk of human error, leading to fewer defects and reworks, which ultimately enhances product reliability.
4. **Scalability**: As businesses grow, so do their production needs. Scalable pipe mill systems allow manufacturers to expand their production lines gradually. Instead of overhauling existing systems, companies can add new components or upgrade existing ones to meet increased demand. This incremental approach helps manage investments efficiently.
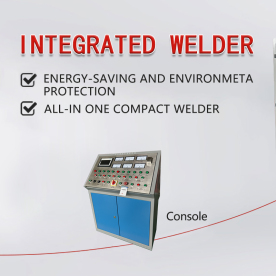
Understanding the Scalable Pipe Mill Production Line System: Enhancements in Efficiency, Flexibility, and Productivity for Modern Manufacturing
5. **Sustainability**: Many modern scalable systems prioritize sustainable manufacturing practices. These systems can optimize resource use—reducing material waste and energy consumption, contributing to greener production practices.
Implementing a Scalable Pipe Mill Production Line
To successfully implement a scalable pipe mill production line, manufacturers should start by assessing their current production capabilities and understanding market demands. This assessment includes identifying potential bottlenecks, evaluating existing machinery, and determining flexibility needs.

Understanding the Scalable Pipe Mill Production Line System: Enhancements in Efficiency, Flexibility, and Productivity for Modern Manufacturing
Working with technology partners can facilitate the selection of appropriate modular machines capable of meeting future demands. Training staff to operate new technologies and adapting processes to integrate automation will also be key steps in the transition.
Finally, it is important for manufacturers to establish a robust feedback loop with customer input. This ongoing dialogue allows businesses to remain aligned with market trends and continuously improve their production line configurations.
Conclusion
The adoption of a Scalable Pipe Mill Production Line System represents a transformative approach to manufacturing in the pipe industry. Its ability to blend efficiency, flexibility, and quality control makes it an invaluable asset for companies striving to maintain competitive advantages. As industry dynamics continue to evolve, manufacturers that invest in scalable systems will be well-positioned to meet future challenges and capitalize on emerging opportunities. With a focus on modular design and state-of-the-art technology, the scalable pipe mill production line is not just a choice—it’s a necessity for success in the modern manufacturing environment.Spare Parts for Tube Mills with Long Service Life