Welding technology has evolved significantly over the past few decades, driven by the need for efficiency, precision, and enhanced joint strength in various industrial applications. Among the many welding techniques available, shear and butt welding stands out as a sophisticated method that provides exceptional results, particularly in the fabrication of metal components. This article aims to explore the advantages of using a shear and butt welder, examining its applications, methodologies, and the benefits it offers to industry professionals.
Understanding Shear & Butt Welding
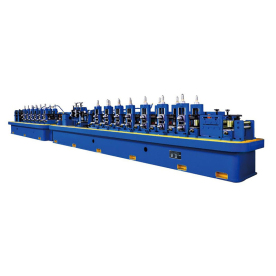
Exploring the Advantages of Shear & Butt Welder Technology in Modern Welding Applications: A Comprehensive Guide for Industry Professionals
Shear and butt welding is a specialized technique used to join two pieces of metal together. The process operates by applying heat and pressure simultaneously to create a weld that is highly resistant to shear forces. This method is particularly effective for metals with high tensile strength, making it a preferred choice in various industries, including automotive, aerospace, and construction.
The shear and butt welder is a machine designed specifically for this process. It comprises precision-engineered components that ensure accurate alignment and consistent performance during welding. The machine effectively combines the elements of shear stress and butt joint configurations to produce strong, durable welds with minimal thermal distortion.
Key Benefits of Shear & Butt Welding
1. **Strength and Durability**: One of the most significant advantages of shear and butt welding is the strength of the joints created. The process generates high bond strength, which minimizes the risk of joint failure under load. This is particularly important in applications where structural integrity is crucial, such as in bridge construction and high-stress mechanical assemblies.
2. **Efficiency and Speed**: Shear and butt welders are designed for high-speed operations, allowing manufacturers to complete projects quickly without sacrificing quality. The automation of the welding process reduces human error and increases throughput, making it an ideal choice for mass production.
3. **Minimal Distortion**: Traditional welding methods can lead to thermal distortion of metal components due to the heat generated during the process. Shear and butt welding, on the other hand, utilizes localized heating and controlled pressure, which significantly reduces the risk of distortion and warping.
4. **Versatility**: Shear and butt welders can be used with a variety of metals, including steel, aluminum, and exotic alloys. This versatility makes it a valuable addition to the toolbox of any fabricator, allowing them to tackle a wide range of projects.
5. **Cost-Effectiveness**: Although the initial investment in a shear and butt welder may be higher than traditional welding equipment, the long-term savings in labor, raw materials, and rework costs make it a cost-effective solution. Additionally, the ability to produce stronger joints means fewer repairs or replacements are needed over time.
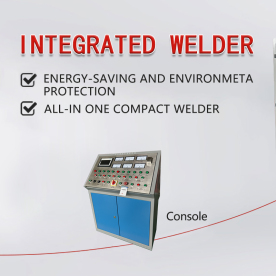
Exploring the Advantages of Shear & Butt Welder Technology in Modern Welding Applications: A Comprehensive Guide for Industry Professionals
6. **Enhanced Safety**: The method reduces the exposure of operators to harmful fumes and heat, consequently improving workplace safety. Advanced welding equipment often includes features such as automated operation and remote monitoring, which further enhances safety protocols.
Applications in Industry
Shear and butt welding is notably prominent in various high-demand sectors:
– **Automotive Manufacturing**: The need for robust and lightweight components has driven the application of shear and butt welders in producing vehicle frames, engine mounts, and body panels. The method’s efficiency is key in high-volume production environments.
– **Aerospace**: In aerospace applications, the strength-to-weight ratio is critical. Shear and butt welding enables the production of structural components that can withstand extreme forces while keeping weight to a minimum.
– **Construction and Fabrication**: With the increasing demand for durable construction elements, shear and butt welding is frequently employed in the fabrication of girders, beams, and other structural components.
Conclusion
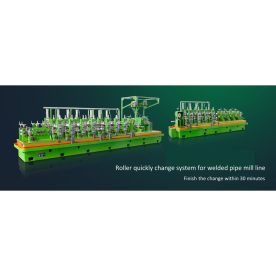
Exploring the Advantages of Shear & Butt Welder Technology in Modern Welding Applications: A Comprehensive Guide for Industry Professionals
The shear and butt welder represents a significant advancement in welding technology, offering a combination of strength, speed, and efficiency that is unmatched in many industrial applications. Its capacity to produce high-quality joints while minimizing distortion and enhancing safety makes it an invaluable tool for professionals in various sectors. As industries continue to seek ways to optimize production while maintaining quality, the adoption of shear and butt welding techniques will likely grow, solidifying its place in the future of manufacturing and fabrication.Tube making machine for stainless steel