In the world of manufacturing, the demand for reliable and efficient welding techniques has never been greater. Among the various welding methods available today, the Shear and Butt Welder stands out as a prominent technology that has transformed the way materials are joined. This article explores the intricacies of shear and butt welding, highlighting its applications, benefits, and importance in modern industrial settings.
**What is Shear & Butt Welding?**
Shear and Butt Welding is a specific type of welding technique that joins two pieces of material end-to-end. The method employs a combination of shear forces and heat to create a strong, permanent bond. Typically used for welding materials such as plastics, metals, or composites, this technique is especially valuable in industries requiring high strength-to-weight ratios and precise manufacturing tolerances.
In sheer welding, extreme pressure is applied to the materials being joined, resulting in a localized melting at the edges of the two pieces. This melting, combined with the force applied, facilitates the fusion of the materials, thereby creating a strong bond once the materials cool down. The butt welding portion of the process refers to the way the materials are aligned—pieces are placed end-to-end and joined seamlessly without any filler metal, ensuring a smooth finish.
**Applications of Shear & Butt Welders**
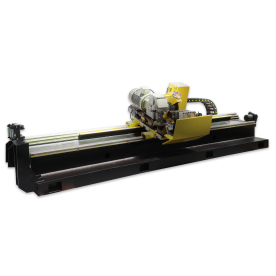
Exploring the Essential Role of Shear & Butt Welder Technology in Modern Manufacturing Processes
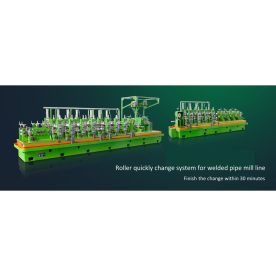
Exploring the Essential Role of Shear & Butt Welder Technology in Modern Manufacturing Processes
Shear and butt welders are utilized across a diverse array of industries, including aerospace, automotive, electronics, and construction. In aerospace, for instance, the lightweight and durable characteristics of components are crucial for fuel efficiency and performance. The high-strength joints produced by shear and butt welding make this technique a preferred choice for airframe and engine parts.
In the automotive industry, butt welding is prominently used for chassis assembly, as it helps in achieving high structural integrity while minimizing weight. The implementation of shear and butt welders greatly improves the assembly line’s efficiency, allowing manufacturers to produce vehicles faster without compromising on safety.
Similarly, the electronics industry benefits from shear and butt welding, especially in the production of circuit boards. The ability to create precise, reliable connections helps ensure the functionality and longevity of electronic components. In construction, shear and butt welders are commonly employed for joining metal beams and supporting structures, enhancing durability and safety standards in buildings and infrastructures.
**Benefits of Using Shear & Butt Welders**
One of the most significant advantages of shear and butt welding is the lack of a need for additional filler materials. This not only saves costs but also reduces the potential for contamination during the welding process. As there are no added materials, the risk of defects, such as porosity or weak joints, is notably lowered. This makes shear and butt welding an efficient and streamlined process.
Another key benefit is the speed of the welding operation. Advanced shear and butt welders can perform welds quickly, increasing productivity on manufacturing lines. The automation of the process also minimizes human error, leading to consistent quality in the final product. Moreover, modern welding machines often incorporate programmable settings, allowing for adaptability when working with various materials and thicknesses.

Exploring the Essential Role of Shear & Butt Welder Technology in Modern Manufacturing Processes
Shear and butt welding also contributes to energy efficiency. The localized heating approach ensures that only the immediate area surrounding the welding joint is affected, which conserves energy compared to other welding techniques that apply heat along the entire length of the materials.
**Challenges and Considerations**
Despite its advantages, shear and butt welding is not without its challenges. One of the primary concerns involves the types of materials being welded. While many metals and plastics can be effectively joined, dissimilar materials can pose difficulties in achieving optimal fusion. Ensuring the materials are compatible in terms of their thermal and physical properties is crucial for a successful weld.
Moreover, the initial setup and calibration of shear and butt welders can be labor-intensive. It requires skilled personnel to set parameters accurately for different welding jobs, which can add to the initial labor costs involved in adopting this welding technique.
**Conclusion**
The Shear and Butt Welder represents a significant advancement in welding technology, offering a blend of efficiency, reliability, and cost-effectiveness across various applications. As industries continue to evolve and demand stronger, lighter, and more durable materials, the role of shear and butt welding in manufacturing processes is poised to grow even further. Understanding the intricacies of this technology not only aids manufacturers in selecting the right welding techniques but also enhances their overall production capabilities in an increasingly competitive market.Spare Parts for Tube Mills with Long Service Life