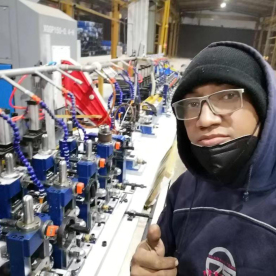
Enhancing Precision and Efficiency in Metal Fabrication: The Advantages of Solid State HF Welder for Thin Metal Sheets
****
In the world of metal fabrication, the quest for precision, efficiency, and quality is paramount. Among the many cutting-edge technologies, the solid state HF welder has emerged as a game-changer, particularly when it comes to welding thin metal sheets. This innovative welding solution leverages high-frequency electromagnetic energy to achieve impressive results with minimal distortion and maximum strength, making it an ideal choice for a variety of industries, including automotive, electronics, and aerospace.
The Mechanics of Solid State HF Welding
Solid state HF welding operates on the principle of high-frequency electromagnetic energy, which is generated using solid-state devices rather than traditional vacuum tubes. This advancement allows for higher reliability, reduced maintenance, and lower operational costs. The process involves bringing two pieces of thin metal sheets together and using the high-frequency waves to generate heat at their interface. As the metal reaches its melting point, the sheets fuse together to create a strong, cohesive bond.
One of the most significant advantages of solid state HF welding is its ability to precisely control the welding parameters, including temperature, pressure, and time. This control is critical when working with thin materials, as excessive heat can lead to warping or burn-through. The ability to finely tune the process ensures that the integrity of the metal sheets is maintained, resulting in high-quality welds that meet demanding specifications.
Benefits of Using Solid State HF Welder for Thin Metal Sheets
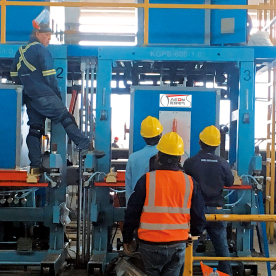
Enhancing Precision and Efficiency in Metal Fabrication: The Advantages of Solid State HF Welder for Thin Metal Sheets
1. **Minimal Distortion and Warping**: Thin metal sheets are often susceptible to distortion during welding processes. Solid state HF welding provides localized heating, which minimizes the overall thermal impact on the material, leading to less warping and higher dimensional accuracy.
2. **High-Speed Welding**: The efficiency of solid state HF welders allows for rapid processing, which is crucial in high-volume manufacturing environments. The ability to produce quality welds in a shorter amount of time means that manufacturers can meet production deadlines without sacrificing quality.
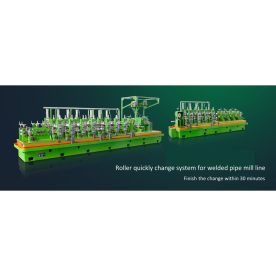
Enhancing Precision and Efficiency in Metal Fabrication: The Advantages of Solid State HF Welder for Thin Metal Sheets
3. **Improved Weld Quality**: The precise energy control of solid state HF welders results in strong, consistent welds. This not only enhances the performance of the final product but also reduces the likelihood of defects that can arise in other welding methods.
4. **Cost-Effectiveness**: Although the initial investment in solid state HF welding technology may be higher than traditional methods, the long-term cost savings are significant. Lower energy consumption, reduced material waste, and decreased rework due to poor weld quality translate into a more favorable return on investment.
5. **Versatility**: Solid state HF welders can be used for a wide range of materials beyond just aluminum and stainless steel, including copper and exotic alloys. This versatility makes them a popular choice for manufacturers looking to optimize their welding capabilities across different applications.
6. **Environmentally Friendly**: The process is cleaner compared to traditional welding methods, generating less smoke and fumes—making it a more environmentally friendly option. This aligns well with the growing emphasis on sustainable practices in manufacturing.
Applications of Solid State HF Welding
The applications of solid state HF welding for thin metal sheets are vast and varied. In the automotive industry, it is commonly used for manufacturing lightweight vehicle components, which are critical in achieving fuel efficiency and emission reduction. In electronics, solid state HF welding is employed in the assembly of components where precision and reliability are essential, such as in circuit boards and connectors. Additionally, its use in the aerospace sector is vital for joining thin materials without compromising safety and performance.
Conclusion
As metal fabrication continues to evolve, the importance of advanced welding technologies cannot be overstated. Solid state HF welders for thin metal sheets offer an innovative approach that addresses many of the challenges faced by manufacturers today. With their precision, efficiency, and ability to produce high-quality welds, these machines are paving the way for more advanced manufacturing processes. As industries increasingly recognize the advantages this technology brings, it is likely to see wider adoption, further enhancing the capabilities of modern metal fabrication.Inductor