****
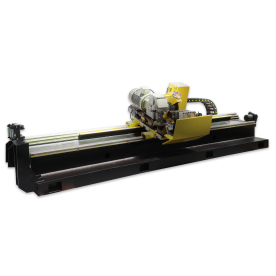
Revolutionizing Sheet Metal Fabrication: The Advantages of Solid State HF Welder for Thin Metal Sheets
In the ever-evolving landscape of metal fabrication and welding, the pursuit of efficiency, precision, and innovation continues to push the industry forward. Among the myriad technologies available for welding applications, the solid state high-frequency (HF) welder stands out as a game-changer, particularly for working with thin metal sheets. As industries increasingly demand high-quality welds with minimal thermal distortion, understanding the benefits and applications of solid state HF welding technology becomes essential for manufacturers and fabricators alike.
The Basics of Solid State High-Frequency Welding
Solid state high-frequency welding is a sophisticated process that primarily employs electromagnetic principles to join materials. Unlike traditional welding methods, which often rely on resistive heating, solid state HF welders use high-frequency electrical energy to generate heat through dielectric heating. This technology enables the rapid joining of thin metal sheets without melting the base materials, ensuring that the structural integrity is largely preserved.
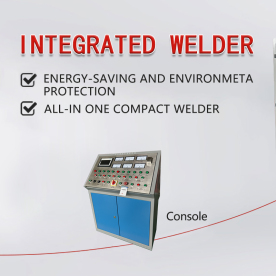
Revolutionizing Sheet Metal Fabrication: The Advantages of Solid State HF Welder for Thin Metal Sheets
The key components of a solid state HF welder include an oscillator that converts standard electrical energy into high-frequency energy, a transformer that increases the voltage, and an electrode assembly that facilitates the welding process. This equipment is designed to operate efficiently with very little energy loss, making it an attractive option for manufacturers seeking eco-friendly solutions.
Advantages of Solid State HF Welding for Thin Metal Sheets
1. **Reduced Heat-Affected Zone (HAZ):** One of the most significant advantages of solid state HF welding is its ability to minimize the heat-affected zone. Traditional welding methods often create large HAZs, leading to warping and changes in material properties. In contrast, HF welding targets the area being welded, ensuring that adjacent areas remain cool and unaltered. This characteristic is especially crucial when working with thin metal sheets, which can easily be distorted or weakened by excessive heat.
2. **Superior Quality Welds:** The precision of solid state HF welding results in superior quality welds. The process allows for consistent and repeatable results, which is vital in industries that require high standards of durability and aesthetics. A low likelihood of defects, such as porosity or inclusions, means that manufacturers can produce more reliable products.
3. **Speed and Efficiency:** Solid state HF welders exhibit remarkable speed compared to traditional welding techniques. The ability to quickly generate heat and achieve a weld makes this technology highly efficient for production environments, where time is often of the essence. The faster turnaround times help suppliers meet demanding schedules without sacrificing quality.
4. **Versatility in Applications:** This welding method is exceptionally versatile, lending itself to a range of applications within various sectors. It is ideal for joining thin metal sheets made from materials such as aluminum, stainless steel, and other alloys. From automotive components to consumer electronics, the adaptability of solid state HF welders makes them an invaluable asset in many production lines.
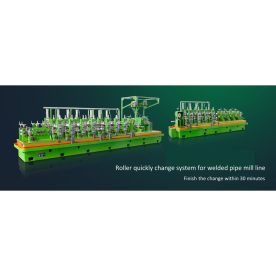
Revolutionizing Sheet Metal Fabrication: The Advantages of Solid State HF Welder for Thin Metal Sheets
5. **Enhanced Energy Efficiency:** Solid state HF welders are designed with energy conservation in mind. Since the process minimizes heat loss, it not only reduces consumed energy but also lowers operational costs. In an age where sustainability is crucial, this energy efficiency aligns with the goals of many manufacturers striving to minimize their carbon footprint.
6. **Automation Compatibility:** The ability to integrate solid state HF welding technology with automated systems enhances its appeal. Automation can streamline production lines, increase throughput, and reduce labor costs. By incorporating this technology into automated processes, manufacturers can optimize their operations further.
Conclusion
As the demand for high-quality, efficient welding solutions grows, the solid state high-frequency welder has emerged as a transformative tool for working with thin metal sheets. Its ability to produce superior quality welds with minimal distortion, combined with its energy efficiency and versatility, positions this technology as a leading option in industries requiring precision and reliability. As fabricators continue to explore the advantages of solid state HF welding, it is evident that this technology will play a crucial role in the future of metal fabrication, setting new standards for excellence and efficiency. The future of welding is here, and it promises to be more innovative than ever before.All-in-one High Frequency Welder with Adjustable Power