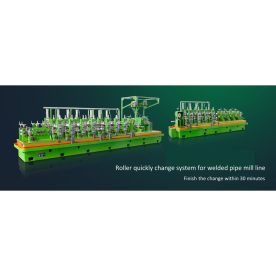
Revolutionizing Welding Efficiency: The Benefits of Solid State HF Welder with Remote Control in Modern Manufacturing
In the ever-evolving world of manufacturing and fabrication, the tools and technology we use continue to shape the efficiency and quality of production processes. One of the most significant advancements in welding technology is the introduction of solid state high-frequency (HF) welders equipped with remote control capabilities. This innovation has not only streamlined welding operations but also enhanced the precision and versatility that modern welding applications demand. In this article, we explore the essential features and benefits of solid state HF welders with remote control, examining their impact on the manufacturing landscape.
Understanding Solid State HF Welding Technology
Solid state HF welders utilize high frequency electrical current to produce heat through resistive heating in materials like metals or plastics. Unlike traditional welding methods that may rely on transformer technology, solid state welders are designed with semiconductor devices that offer greater efficiency, control, and reliability. These welders are particularly effective for applications requiring high-speed welding and consistent quality, making them a popular choice for industries ranging from automotive to aerospace.
The Role of Remote Control in Welding
The integration of remote control functionality in solid state HF welders represents a significant leap forward in the way welding is conducted. Remote control capabilities allow operators to adjust settings, monitor progress, and manage multiple welding stations from a distance, leading to several key advantages:
1. **Increased Operator Safety**: Welding can involve hazardous conditions, including exposure to high heat, toxic fumes, and heavy machinery. By enabling remote control, operators can maintain a safe distance from the welding zone, reducing the risk of accidents and injuries.
2. **Enhanced Precision and Control**: Remote control systems often come equipped with digital interfaces that provide precise control over welding parameters such as temperature, pressure, and time. This level of control ensures that welds are consistent and of superior quality, minimizing defects and rework.
3. **Improved Workflow and Efficiency**: The ability to control multiple welders remotely allows for better resource allocation and workflow optimization. Operators can easily switch between tasks or adjust settings on-the-fly without the need to physically approach each welding unit. This flexibility leads to higher productivity and reduced downtime.

Revolutionizing Welding Efficiency: The Benefits of Solid State HF Welder with Remote Control in Modern Manufacturing
4. **Data Monitoring and Analytics**: Many modern remote-controlled solid state HF welders come with advanced monitoring systems that collect data on various aspects of the welding process. This data can be analyzed to identify trends, optimize processes, and enhance overall production efficiency. Real-time monitoring also allows for immediate adjustments, further improving the quality of welds.

Revolutionizing Welding Efficiency: The Benefits of Solid State HF Welder with Remote Control in Modern Manufacturing
Benefits of Solid State HF Welders with Remote Control
The combination of solid state technology and remote capabilities offers numerous benefits that can greatly enhance manufacturing processes:
– **Energy Efficiency**: Solid state welders are known for their energy efficiency compared to traditional welding systems. By using less power while maintaining high performance levels, businesses can reduce operational costs and minimize their carbon footprint.
– **Versatility**: These welders can easily handle a wide range of materials and thicknesses, making them suitable for various applications. The added remote control feature allows operators to adapt settings quickly according to the specific requirements of each project.
– **Reduced Maintenance**: Solid state welders typically require less maintenance than their conventional counterparts. With fewer moving parts and enhanced cooling systems, they are designed to operate reliably over extended periods, leading to lower maintenance costs.
– **Scalability**: As manufacturing demands grow, the ability to integrate additional welding stations or expand operations is essential. Remote-controlled solid state HF welders can be easily scaled up, ensuring that manufacturers can meet increased demands without compromising quality or safety.
Conclusion
The introduction of solid state HF welders with remote control has fundamentally transformed the welding landscape, offering significant improvements in safety, efficiency, and quality. As industries continue to seek innovative solutions to enhance productivity and meet growing demands, these advanced welding systems stand out as a critical investment for modern manufacturers. With their energy efficiency, precision control, and ability to optimize workflow, solid state HF welders equipped with remote capabilities are paving the way for a more efficient future in manufacturing.Mould for tube mill