****
In the ever-evolving field of metallurgy and manufacturing, the demand for efficient, reliable, and precise joining methods continues to escalate. One cutting-edge technology that has garnered significant attention is the solid state high frequency welder machine. This innovative device not only enhances the quality of welding but also offers remarkable advantages over traditional welding techniques. In this article, we will delve into the functioning, applications, and benefits of solid state high frequency welding, positioning it as a game-changer in the industry.
**Understanding Solid State High Frequency Welding**
Solid state high frequency welding, often referred to as high-frequency induction welding, leverages electromagnetic energy to heat and bond materials at a molecular level. Unlike conventional welding methods that rely on the application of high heat through direct flame or arc, this technique uses high-frequency alternating currents to generate heat through resistance in the materials being welded.
The process begins by placing the metal components between electrodes, which are connected to the high-frequency welder machine. As the electromagnetic field is applied, the materials heat up rapidly — enabling them to reach the melting point necessary for joining — without requiring excessive pre-heating or post-welding processing. One of the standout features of solid state high frequency welders is their ability to achieve extremely localized heating, making them particularly effective for delicate and thin metal workpieces.
**Key Advantages of Solid State High Frequency Welders**
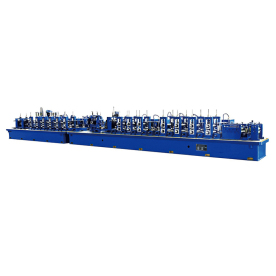
Innovating the Future of Metal Joining with Solid State High Frequency Welder Machines: A Comprehensive Overview
1. **Precision and Control**: One of the paramount benefits of solid state high frequency welder machines is the level of control they provide over the welding process. Operators can precisely manage the temperature and time, resulting in consistent weld quality. This precision minimizes the risk of warping or distortion of the workpieces, an issue that often plagues traditional welding methods.
2. **Clean and Efficient Operation**: High-frequency welding is a clean process that generates minimal waste. There are no fumes or spatter associated with gas welding, making it a safer and more environmentally friendly option. Additionally, this welding method often leads to quicker cycle times, enhancing overall operational efficiency.
3. **Versatility Across Materials**: Solid state high frequency welders are suitable for a variety of materials, including steel, aluminum, copper, and specialty alloys. Their adaptability makes them an essential tool in diverse industries, including automotive, aerospace, electronics, and piping manufacturing.
4. **Energy Efficiency**: The design of solid state high frequency welding machines emphasizes energy efficiency. By focusing energy specifically where it is needed for the weld, these machines consume significantly less power compared to traditional welding methods, all while achieving superior outcomes.
5. **Reduced Labor and Operational Costs**: With the improved efficiency and speed of solid state welding, companies can enjoy lower labor costs and increased throughput. The automation capabilities of modern solid state high frequency welders further streamline operations, allowing fewer operators to handle higher volumes of welding tasks.
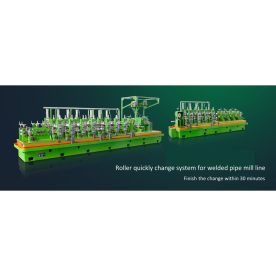
Innovating the Future of Metal Joining with Solid State High Frequency Welder Machines: A Comprehensive Overview
**Applications of Solid State High Frequency Welders**
The applications of solid state high frequency welding are vast and varied. In the automotive industry, this technology is often applied to create high-strength, lightweight components that are essential for modern vehicle design. Aerospace manufacturing also benefits from the precision of solid state welding, particularly in the creation of fuel tanks and lightweight structural elements.

Innovating the Future of Metal Joining with Solid State High Frequency Welder Machines: A Comprehensive Overview
In electronics, solid state high frequency welders are used to create reliable connections in circuit boards and semiconductor packaging. The medical device industry leverages this technology for its ability to join delicate components without compromising their integrity. Additionally, the piping and tubing sectors utilize solid state welding for robust and leak-proof joints in critical applications such as oil and gas transport.
**Conclusion**
As industries seek to innovate and improve efficiency in their manufacturing processes, solid state high frequency welder machines emerge as a vital tool in modern metallurgy. With their precision, cleanliness, energy efficiency, and versatility, these machines are not merely a trend but a fundamental shift in how materials are joined. As technology continues to advance, the adoption of solid state high frequency welding promises to become even more widespread, paving the way for a new era of manufacturing excellence.Stainless steel pipe mill production line