****
In the evolving landscape of manufacturing, the introduction of advanced welding technologies has redefined how industries approach metal joining processes. One of the most significant innovations in this domain is the solid state high frequency welder, a tool that has transformed the efficiency, quality, and versatility of welding applications. This article will delve into what solid state high frequency welders are, their advantages over traditional welding methods, and their implications for the future of manufacturing.
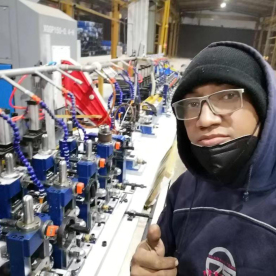
Revolutionizing Manufacturing Processes: The Impact of Solid State High Frequency Welders on Modern Fabrication Techniques
Solid state high frequency welding is a process that uses high-frequency electric currents to create a weld at the interface of two pieces of metal. Unlike conventional welding methods that rely on heat generated by arc or flame, solid state welding is a more efficient approach that often results in improved weld integrity and reduced thermal distortion. The basic principle behind this technology is the Joule heating effect, wherein high-frequency currents produce localized heating at the contact point between the metal surfaces, ensuring a clean and effective bond.
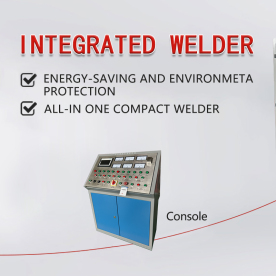
Revolutionizing Manufacturing Processes: The Impact of Solid State High Frequency Welders on Modern Fabrication Techniques
One of the standout features of solid state high frequency welders is their ability to achieve excellent control over the welding parameters, such as pressure, frequency, and temperature. This level of precision is crucial when working with delicate materials or intricate designs, making these welders particularly valuable in sectors like aerospace, automotive, and electronics. The precise control of the welding process minimizes the risk of defects, reducing the need for post-weld inspection and rework, which can be both time-consuming and costly.
The advantages of solid state high frequency welders are numerous. First and foremost, they are highly efficient. The process does not require extensive pre-heating or post-heating, which can significantly expedite production timelines. Manufacturers can produce parts at a quicker rate, allowing for increased output and a more streamlined workflow. Moreover, less energy consumption means that businesses can reduce their operational costs and carbon footprint, aligning with the growing emphasis on sustainability in manufacturing.
Another significant benefit is the reduction of heat-affected zones (HAZ). Traditional welding methods can create wider HAZ, which may compromise the mechanical properties of the surrounding material. In contrast, solid state welding generates a much smaller HAZ, which helps preserve the integrity of the base materials. This characteristic is particularly crucial in industries where material performance is paramount, such as in the production of high-stress components for aircraft or automotive applications.
The versatility of solid state high frequency welders further enhances their appeal. They are capable of welding a wide range of metals, including stainless steel, copper, and aluminum, making them an ideal choice for manufacturers who work with various materials. Additionally, they can be employed in different configurations, from lap to butt welding, adapting to specific manufacturing needs and designs.
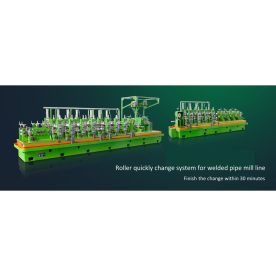
Revolutionizing Manufacturing Processes: The Impact of Solid State High Frequency Welders on Modern Fabrication Techniques
As technology continues to advance, the integration of automation and smart technologies into solid state high frequency welders is paving the way for the future of manufacturing. Automated welding systems equipped with sensors and data analytics can optimize the welding process in real time, further enhancing efficiency and quality control. This level of sophistication can help manufacturers meet increasing demands for precision and reliability in their products while simultaneously lowering labor costs.
Cost considerations, however, do play a significant role in the adoption of solid state high frequency welders. The initial investment for these systems may be substantial, which can be a barrier for smaller enterprises. Yet, when evaluating the total cost of ownership, including operational efficiencies, reduced waste, and lower rework rates, it becomes clear that the long-term benefits often outweigh the initial expenditures.
In conclusion, the advent of solid state high frequency welders represents a significant advancement in welding technology. By providing enhanced efficiency, reduced heat-affected zones, and the ability to weld a variety of materials, these machines are poised to transform manufacturing processes across multiple industries. As the pursuit of higher quality and more sustainable practices continues, solid state high frequency welding stands at the forefront, promising innovations that will shape the future of fabrication. Transitioning into this next era of manufacturing may very well depend on the capabilities and efficiencies that solid state high frequency welders bring to the table.Industrial-grade All-in-one Welder