In the world of manufacturing, particularly in industries that rely heavily on tube mills, the importance of specialized spare parts cannot be overstated. Large-scale tube mills are critical assets for producing a variety of metal tubes and pipes used in construction, automotive, and various other sectors. The efficiency and longevity of these machines significantly depend on the quality and availability of their specialized spare parts. In this article, we delve into the various components that make up these mills, the significance of using specialized spare parts, and the impact they have on operational efficiency.
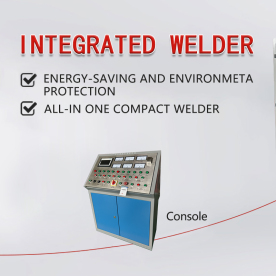
Understanding the Importance of Specialized Spare Parts for Large-Scale Tube Mills: Ensuring Efficiency and Longevity in Manufacturing Processes
Understanding Large-Scale Tube Mills
Large-scale tube mills are complex machines designed for the high-speed production of tubular products. These mills utilize a series of rollers and forming stations to shape metal strips into tubes, which are then welded together, often through high-frequency welding techniques. The process involves multiple stages, including strip preparation, tube formation, welding, cooling, and cutting to length. Given their intricate nature and the demands of continuous production, maintaining optimal performance in these mills is crucial.
The Role of Specialized Spare Parts
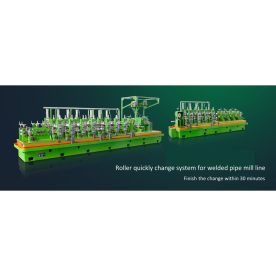
Understanding the Importance of Specialized Spare Parts for Large-Scale Tube Mills: Ensuring Efficiency and Longevity in Manufacturing Processes
Specialized spare parts are essential for ensuring that large-scale tube mills function efficiently and remain operational over extended periods. Unlike standard spare parts, which may fit a variety of machines, specialized parts are specifically designed to meet the unique requirements of tube mills. This specialization includes considerations for material specifications, dimensions, tolerances, and performance characteristics that are tailored to withstand the operational stresses experienced during the manufacturing process.
Key Components of Tube Mills
The main components of large-scale tube mills that often require specialized spare parts include:
1. **Rollers**: Rollers are critical in shaping the metal strip into a tube. Wear and tear over time can lead to defects in the product or downtime during production. Specialized rollers made from resistant materials and precise engineering specifications are vital for maintaining quality.
2. **Welding Equipment**: The welding process in tube mills is typically one of the most demanding stages. Spare parts for welding machines, including electrodes and nozzles, must be designed to handle high temperatures and pressures.
3. **Bearings and Shafts**: Bearings are essential for the smooth operation of rotating components in the mill. Over time, they can wear down, leading to increased friction and energy consumption. Specialized bearings that account for load, speed, and environmental conditions are crucial for minimizing downtime.
4. **Drive Motors and Gearboxes**: The motors and gearboxes transmit power to drive the mill. Specialized parts for these components ensure efficient power transfer and reduce the likelihood of failure.
5. **Cooling Systems**: The cooling systems are vital for maintaining optimal temperatures during production. Specialized components in the cooling system, such as pumps and valves, must be able to endure specific pressure and temperature ranges.
Benefits of Using Specialized Spare Parts

Understanding the Importance of Specialized Spare Parts for Large-Scale Tube Mills: Ensuring Efficiency and Longevity in Manufacturing Processes
1. **Enhanced Performance**: Specialized spare parts are designed to fit perfectly and perform optimally within tube mills, resulting in enhanced operational performance. This leads to reduced downtime and increased production rates.
2. **Increased Longevity**: High-quality specialized parts are engineered for durability, reducing the frequency of replacements and maintenance. This translates to lower operational costs over time.
3. **Improved Safety**: Using parts specifically designed for tube mills mitigates the risk of machinery failures that can lead to workplace accidents. Improved safety not only protects workers but also minimizes potential liabilities for manufacturers.
4. **Customization**: Many manufacturers benefit from custom-engineered spare parts tailored to their specific processes and machinery. This allows for better alignment of the parts with production requirements, improving efficiency.
5. **Reduced Energy Consumption**: Well-maintained equipment with high-quality parts operates more efficiently, consuming less energy. This reduction is not only cost-effective but also environmentally beneficial, aligning with modern sustainability goals.
Conclusion
The reliance on specialized spare parts for large-scale tube mills has become increasingly important in today’s fast-paced manufacturing landscape. Investing in these parts ensures that machinery operates effectively, performs reliably, and maintains production standards. As industries evolve and demand for precision and quality increases, the role of specialized spare parts will only grow, solidifying their place as a cornerstone in the efficient operation of tube mills. By prioritizing quality and specialization, manufacturers can secure their competitive edge and streamline their operations for sustained success.High-Quality Spare Parts for Cold Cutting Saw Machines