****
In today’s fast-paced industrial landscape, efficiency and precision are key drivers of success. Among the various tools that support these goals, one notable innovation is the tube making machine with cutting function. This advanced piece of machinery is transforming the way manufacturers approach tube production, leading to improvements in quality, cost reduction, and overall workflow efficiency.
Understanding Tube Making Machines
Before diving into the cutting function and its advantages, it’s essential to understand what tube making machines do. These machines are specifically designed to produce tubes from a variety of raw materials, such as metal, plastic, and other composites. The manufacturing process typically involves several stages, including material feeding, shaping, welding or bonding, and, crucially, cutting.
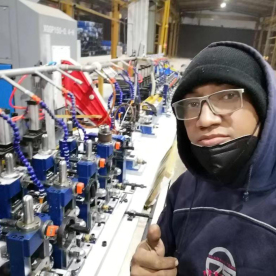
Revolutionizing Manufacturing: The Advantages of Tube Making Machines with Cutting Functionality for Efficient Production
Tube making machines have evolved over the years, incorporating advanced technologies such as computerized controls and automation. This evolution has not only boosted production speeds but has also enhanced the quality of the final product. Every tube produced must meet specific requirements regarding dimensions, strength, and finish, making precision-critical.
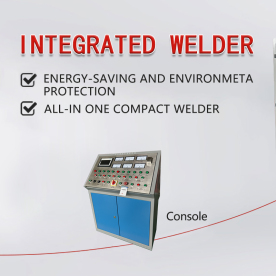
Revolutionizing Manufacturing: The Advantages of Tube Making Machines with Cutting Functionality for Efficient Production
The Cutting Function and Its Importance
The cutting function of a tube making machine plays a vital role in the production process. After the tube has been formed, it needs to be cut to specific lengths to meet customer specifications or to fit into further processing systems. The cutting function ensures that this process is not only accurate but also done quickly and efficiently.
1. **Precision Cutting:** One of the most significant advantages of integrated cutting capabilities is precision. Traditional methods of tube cutting often involved secondary processes that could introduce errors and inconsistencies. However, a tube making machine with a cutting function allows for simultaneous shaping and cutting, minimizing the margin for error. This precision is particularly critical in industries such as aerospace, automotive, and medical, where standards are stringent, and even minor deviations can lead to failure in applications.
2. **Increased Efficiency:** Incorporating cutting directly into the tube forming process streamlines production. Manufacturers no longer need to transfer products to another machine for cutting, which can introduce additional handling, potential damage, and wasted time. This one-stop production reduces lead times significantly, allowing companies to respond quickly to market demands. Faster production cycles mean that businesses can fulfill larger orders or introduce new products without the usual delays.
3. **Cost Reduction:** With increased efficiency comes cost savings. By reducing the number of machines and processes required to manufacture tubes, manufacturers can lower their operational costs. Fewer machines also mean less maintenance and lower energy consumption, all contributing to a leaner manufacturing process. Additionally, enhanced accuracy reduces waste material, further driving down production costs.
4. **Versatility:** Tube making machines with integrated cutting functionality can be programmed to handle various materials and tube designs. This versatility allows manufacturers to meet diverse customer requirements without investing in multiple machines for different tasks. Whether producing small tubes for intricate applications or large pipes for industrial use, these machines can adapt, making them invaluable assets in modern manufacturing.
5. **Quality Control:** The integration of cutting functions within the tube production process enhances quality control by allowing real-time monitoring. Advanced tube making machines can utilize sensors and software to ensure the cutting complies with specified dimensions and tolerances throughout the process. Manufacturers can quickly identify and rectify issues without halting production, leading to higher quality products and increased customer satisfaction.
Conclusion
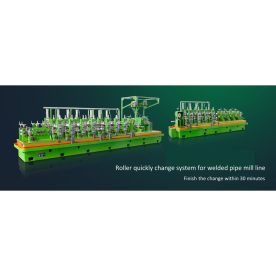
Revolutionizing Manufacturing: The Advantages of Tube Making Machines with Cutting Functionality for Efficient Production
The tube making machine with cutting function is a transformative technology in the manufacturing sector. Its precision, efficiency, and cost-saving capabilities make it a crucial investment for companies looking to maintain competitiveness in the global market. As industries continue to evolve and grow, this innovative machinery not only meets existing needs but also paves the way for future advancements. Embracing this technology can position manufacturers to not only thrive today but also prepare for the challenges and opportunities of tomorrow.Precision ERW tube mill machinery