In the fast-evolving landscape of manufacturing, efficiency and precision are paramount. As industries strive to enhance productivity while maintaining quality, one piece of equipment stands out: the tube making machine with cutting function. This innovative technology is transforming the way various sectors operate, offering a seamless integration of tube manufacturing and cutting processes that meet the varying demands of modern production lines.
Understanding Tube Making Machines
Before delving into the cutting functions, it’s essential to understand what a tube making machine is. These machines are designed to produce a wide array of tube shapes and sizes from various materials, including metals, plastics, and composites. The manufacturing process typically involves forming, welding, and finishing operations to create high-quality tubes suitable for numerous applications, ranging from structural components in construction and automotive industries to specialized tubes used in medical devices.
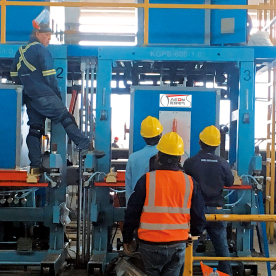
Revolutionizing Manufacturing: The Role of Tube Making Machines with Cutting Functions in Modern Industries
The Importance of Cutting Functions
Traditionally, tube manufacturing involves separate machines for forming the tube and subsequently cutting it to specific lengths. This separation can lead to inefficiencies, increased labor costs, and higher chances of errors during the transfer process. Tube making machines equipped with cutting functions have effectively addressed these challenges by consolidating both processes into a single unit.
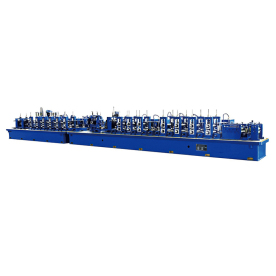
Revolutionizing Manufacturing: The Role of Tube Making Machines with Cutting Functions in Modern Industries
The cutting function is particularly significant in industries where precision is crucial. For instance, creating tubes for aerospace or automotive applications requires stringent adherence to specifications to ensure safety and performance. A machine that can both create and cut tubes accurately eliminates discrepancies that may arise when using separate machines.
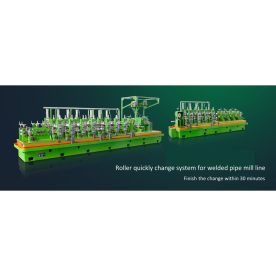
Revolutionizing Manufacturing: The Role of Tube Making Machines with Cutting Functions in Modern Industries
Types of Cutting Functions
The cutting functions of tube making machines can vary significantly. Generally, they include:
1. **Rotary Cutting**: This method involves using a rotary blade that spins at high speeds, rapidly cutting through tubes with precise dimensions. It’s beneficial for high-speed production runs where maintaining consistent lengths is vital.
2. **Shearing**: Involves a cutting blade that slides across the tube without rotation. This method is beneficial for thick tubes or certain materials that may not be ideal for rotary cutting.
3. **Laser Cutting**: A more advanced option, laser cutting offers unparalleled precision. This method utilizes a focused laser beam to cut through materials, making it ideal for intricate designs and tight tolerances.
4. **Plasma Cutting**: Similar to laser cutting but employs plasma to achieve high temperatures, melting through thick materials quickly. It’s often used in industrial applications where heavy-duty tubes are required.
Benefits of Integrated Tube Making Machines with Cutting Functions
1. **Enhanced Efficiency**: By integrating the cutting function into the tube making machine, manufacturers can significantly reduce cycle times. The combined operations eliminate the need for manual handling between processes, thereby cutting down on labor hours and minimizing the risk of damaging products during transfer.
2. **Cost Savings**: With fewer machines needed on the production floor and reduced manpower for operations, companies can realize substantial cost savings. The maintenance of a single machine is also more manageable compared to maintaining multiple pieces of equipment.
3. **Quality Assurance**: Integrated tube making machines typically come equipped with advanced monitoring systems that can check for quality throughout the manufacturing process. This capability ensures that any defects in the tube or cutting process are identified and rectified in real-time, thus maintaining high-standard production.
4. **Flexibility and Adaptability**: Modern tube making machines with cutting functions often come with programmable features that allow manufacturers to easily switch between different tube sizes and types. This adaptability is crucial for companies that need to respond quickly to market demands or custom orders.
5. **Space Efficiency**: As manufacturing spaces become tighter and more valuable, consolidating processes into a single machine allows for better use of floor space. This efficiency is particularly important in smaller workshops or factories where every square foot counts.
Conclusion
The tube making machine with cutting function represents a significant advancement in manufacturing technology. With the ability to streamline production, enhance precision, and reduce costs, these machines are increasingly becoming a staple in industries worldwide. As technology continues to progress, the integration of such advanced machines will likely play an even more crucial role in shaping the future of manufacturing, pushing the boundaries of what’s possible in various sectors. By adopting these innovations, manufacturers can not only meet today’s demands but also prepare for the challenges of tomorrow.Cold Cutting Saw Machine Replacement Parts