****
In the world of manufacturing and steel processing, tube mills play a crucial role in fabricating tubular products that are integral to various industries, from automotive to construction. Given the critical nature of these machines, ensuring their efficiency and longevity through routine maintenance and the timely replacement of worn-out parts is essential. This article delves into the importance of tube mill replacement parts, the common components that require replacement, and tips for maintaining your tube mill system for optimal performance.
Understanding Tube Mills
Tube mills are specialized machinery used to produce a wide range of tubular products, including pipes and tubes made from metal. These machines typically operate through a series of stages, beginning with the feeding of metal strips, which are then formed into a tube shape. Following this, they undergo welding, sizing, and cutting processes to achieve the desired specifications. Given their continuous operation in high-stress environments, tube mills are susceptible to wear and tear, making it imperative to monitor their components regularly.
Importance of Replacement Parts
The timely replacement of tube mill parts is central to maintaining productivity and ensuring that the mills operate at peak performance. Neglecting to replace worn-out components can lead to a cascade of issues, including reduced output quality, increased downtime, and even severe damage to the machine itself. This can result in costly repairs and extended periods of halted production, which can significantly affect a company’s bottom line.
Common Replacement Parts in Tube Mills
1. **Rolls and Roll Stands:** The rolls are instrumental in shaping and forming the metal strips into tubes. Over time, these rolls can become worn down, leading to inaccuracies in tube dimensions and surface finishes. Regular inspection and timely replacement of rolls are critical to ensuring the quality of the finished product.
2. **Bearings:** Bearings facilitate the smooth rotation of various components within the tube mill. Damaged or worn bearings can result in increased friction and heat, leading to further complications and potential machine failure. Regular lubrication and proactive replacement of bearings can extend their lifespan significantly.
3. **Welders:** The welding stage is vital for ensuring that the edges of the formed tubes bond seamlessly. Failures in the welding machine can lead to weak joints, affecting the overall integrity of the product. Replacement parts for welders should be readily available to ensure quick repairs and minimal production interruptions.
4. **Guards and Chokers:** These components help maintain the desired shape and guide the material through the mill. Over time, guards and chokers may become damaged or misaligned, leading to production inefficiencies and product defects. Regular inspection and maintenance are essential to ensure these components are functioning as intended.
5. **Cut-off Blades and Sizing Rolls:** As the final stages in the tube mill process, cut-off blades and sizing rolls must maintain precision to ensure the finished product meets specifications. Worn-out blades can lead to poor cuts, while sizing rolls that are out of tolerance can affect the final diameter and wall thickness of the tubes.
Maintaining Tube Mill Components
To ensure the longevity and effectiveness of tube mill replacement parts, certain maintenance practices should be adhered to:
1. **Routine Inspections:** Implement a schedule for regular inspections of all vital components. Early detection of wear can prevent more extensive damage and expensive repairs.
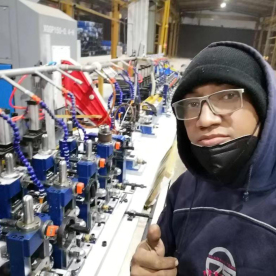
A Comprehensive Guide to Tube Mill Replacement Parts: Ensuring Optimal Performance and Longevity of Your Tube Mills
2. **Scheduled Maintenance:** Develop a comprehensive maintenance program that includes lubrication schedules, component replacements, and alignment checks to maintain operational efficiency.

A Comprehensive Guide to Tube Mill Replacement Parts: Ensuring Optimal Performance and Longevity of Your Tube Mills
3. **Quality Replacement Parts:** Invest in high-quality replacement parts from reputable suppliers. Using substandard parts can lead to premature failure and may not provide the reliability needed in a demanding manufacturing environment.
4. **Training Operators:** Ensure that machine operators are well-trained in the proper operation and maintenance of tube mills to minimize the risk of human error, which can lead to premature component wear.

A Comprehensive Guide to Tube Mill Replacement Parts: Ensuring Optimal Performance and Longevity of Your Tube Mills
Conclusion
Understanding the importance of tube mill replacement parts and maintaining the machinery properly can greatly enhance the productivity and efficiency of manufacturing operations. By regularly inspecting components, investing in quality replacements, and adhering to proactive maintenance practices, manufacturers can ensure that their tube mills remain in optimal working condition, delivering high-quality products with minimal downtime.Energy-saving induction heating equipment