****
In the world of manufacturing, efficiency and productivity often dictate the success or failure of a business. With the increasing demand for high-quality tubing products, tube mills play an essential role in delivering the precision and reliability that customers expect. However, to maintain this level of output, it is critical to prioritize the upkeep and replacement of tube mill spare parts. This article delves into the significance of these components in ensuring enhanced efficiency within tube mill operations.
The Role of Tube Mill Spare Parts
Tube mills operate with a series of mechanical components that work in unison to produce seamless tubes and other tubular products. These components include rolls, bearings, conveyor belts, and welders, among others. Over time, wear and tear are inevitable, regardless of the quality of the initial materials used. This is where tube mill spare parts come into play.
By providing reliable replacements, spare parts help maintain the integrity of the tube mill’s operation. A well-maintained machine not only minimizes downtime but also promotes a consistent production flow, resulting in higher output and, ultimately, greater profitability. The importance of sourcing high-quality spare parts cannot be overstated; low-quality substitutes can lead to more significant issues and unexpected failures.
Benefits of Using Quality Spare Parts
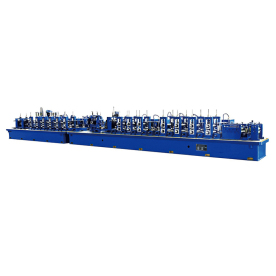
Boost Your Manufacturing Operations: The Importance of Tube Mill Spare Parts for Enhanced Efficiency and Productivity
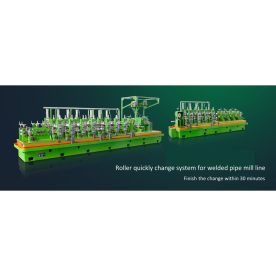
Boost Your Manufacturing Operations: The Importance of Tube Mill Spare Parts for Enhanced Efficiency and Productivity

Boost Your Manufacturing Operations: The Importance of Tube Mill Spare Parts for Enhanced Efficiency and Productivity
1. **Reduced Downtime and Increased Productivity** One of the most immediate benefits of using high-standard tube mill spare parts is the reduction in unexpected machinery breakdowns. When parts wear out, it can lead to unplanned downtime, which disrupts the manufacturing process. By investing in high-quality spare parts, manufacturers can ensure that replacement components last longer and operate more reliably, thereby maintaining continuous production cycles.
2. **Cost-Effectiveness** While it may be tempting to cut costs by purchasing cheaper spare parts, this approach often backfires. Inferior parts are more prone to failure, leading to constant replacements and repairs that can accumulate significant costs over time. Investing in quality spare parts may require a higher initial outlay, but they often prove to be more cost-effective in the long run as they help avoid frequent breakdowns and maintenance expenses.
3. **Enhanced Quality Control** Quality spare parts contribute to enhanced product quality. In the manufacturing of tubes, precision is critical. Any inconsistency in component performance—such as misalignments created by faulty bearings—can result in defective products. Utilizing high-quality and precise spare parts helps maintain the integrity of the entire process and ensures that the products produced meet the required standards.
4. **Better Energy Efficiency** Machines that operate with worn or subpar components can consume more energy, resulting in inflated operational costs. By upgrading to efficient and well-maintained spare parts, manufacturers can reduce energy consumption, leading to lower electricity bills and an overall smaller carbon footprint.
The Importance of Regular Maintenance
Adopting a proactive maintenance strategy can significantly affect the performance of tube mills. Regular inspections and timely replacements of spare parts keep the machines in optimal condition. A well-structured maintenance schedule could involve daily checks for signs of wear, quarterly deep-dive inspections, and annual overhauls to replace all critical spare parts pre-emptively.
Additionally, routine maintenance aids in identifying potential issues before they become significant problems. This not only enhances equipment longevity but also fosters a culture of safety in the workplace, minimizing workplace accidents related to machinery failures.
Conclusion
In conclusion, tube mill spare parts are not just components of the machinery; they are vital elements that underpin overall manufacturing efficiency and productivity. Investing in high-quality spare parts, coupled with a structured maintenance strategy, can lead to reduced downtime, enhanced product quality, and increased operational effectiveness. Manufacturers seeking to thrive in a competitive landscape must prioritize these factors to ensure they meet the demands of their customers while maximizing profitability. The benefits of enhanced efficiency extend beyond the manufacturing floor—they can lead to increased customer satisfaction, stronger market positioning, and overall business growth.Customized ERW tube mill solutions