In the realm of modern manufacturing, particularly in the metal fabrication industry, the uncoiler plays a pivotal role that is often overlooked. An uncoiler is a machine designed to unwind coils of metal or other materials so that they can be processed further, shaped, or cut to size. This process is integral in ensuring that production runs smoothly and efficiently, and the benefits of utilizing an uncoiler can greatly enhance the overall workflow in a manufacturing facility.
To understand the importance of uncoilers, it is critical to first examine their function within manufacturing operations. Manufacturers often receive materials in coil form, whether it be steel, aluminum, or other metals. These coils are typically heavy and can be cumbersome to handle manually. The uncoiler mechanizes the process of unwinding these coils, allowing for a continuous supply of material to feeding machines, such as shears, roll formers, and press brakes. This not only saves time and labor but also improves safety by minimizing the need for manual handling of heavy loads.
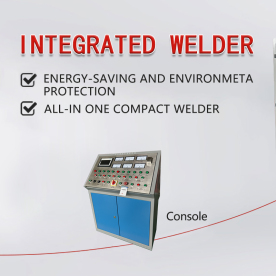
The Essential Role of Uncoilers in Modern Manufacturing Processes: Enhancing Efficiency and Precision in Metal Fabrication
Uncoilers come in various designs and sizes, tailored to fit specific applications and the dimensions of the material being processed. Some uncoilers are designed for lighter materials, while others are equipped to handle much heavier coils. They can be powered by electric motors, hydraulic systems, or even pneumatic mechanisms, depending on the requirements of the manufacturing process. Advanced models come with features such as automatic feeding systems, tension control, and even integration into larger automated production lines, which significantly streamlines operations.
One of the main advantages of using an uncoiler is that it significantly boosts operational efficiency. By automating the unwinding process, manufacturers can reduce the time spent on setting up machinery and handling material. In industries where speed and precision are imperative, such as automotive or aerospace manufacturing, uncoilers ensure that operations remain uninterrupted, increasing production rates and meeting tight deadlines. With an uncoiler in place, the time-consuming task of manually feeding coils into processing machines is eliminated, allowing operators to focus on more critical aspects of the manufacturing process.
Another crucial aspect of uncoilers is their ability to improve product quality. When materials are unwound manually, the risk of introducing defects increases. Improper handling can lead to material deformities, surface scratches, or unintentional bending, which in turn affects the final product quality. However, with an uncoiler, the material is unwound uniformly and at a controlled rate, minimizing the chance of damage during the process. This precision leads to fewer errors and defects in the final products, thereby reducing waste and improving customer satisfaction.
Moreover, the integration of uncoilers with modern automation technologies has led to an even more significant enhancement in manufacturing processes. Many uncoilers can be seamlessly connected to other equipment, creating a fully automated production line. This integration allows for real-time monitoring and control of material flow, further optimizing the manufacturing process. Manufacturers can track usage rates, manage inventory effectively, and make necessary adjustments to production schedules without any downtime. Such technological advancements represent a remarkable shift from traditional manufacturing methods, making it easier for companies to adapt to changing market demands.
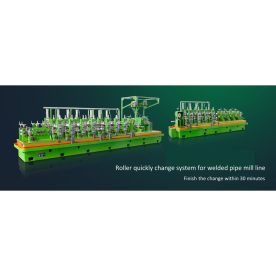
The Essential Role of Uncoilers in Modern Manufacturing Processes: Enhancing Efficiency and Precision in Metal Fabrication

The Essential Role of Uncoilers in Modern Manufacturing Processes: Enhancing Efficiency and Precision in Metal Fabrication
In summary, the uncoiler is an indispensable tool in today’s fast-paced manufacturing environment. By improving efficiency, enhancing product quality, and enabling seamless integration into automated production lines, uncoilers have proven to be a vital component in the metal fabrication industry and beyond. As manufacturers continue to seek ways to improve their operations and stay competitive, the role of uncoilers will undoubtedly become even more prominent. Companies that invest in this technology not only optimize their production processes but also position themselves to meet the evolving needs of their customers in a constantly changing marketplace.Original Spare Parts for Tube Mills