In the ever-evolving landscape of modern manufacturing, machinery has transformed the way businesses operate, pushing the boundaries of efficiency and precision. One such essential piece of equipment that plays a vital role in material handling is the uncoiler. Designed to feed coils of raw materials such as metal and plastic into the manufacturing process, the uncoiler is indispensable in various industries, including automotive, aerospace, and construction. This article delves into the importance of uncoilers, their operational mechanisms, and how they contribute to overall manufacturing efficiency.
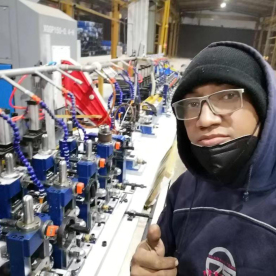
Understanding the Role of an Uncoiler in Modern Manufacturing: Efficiency and Precision in Material Handling and Processing
The Functionality of an Uncoiler
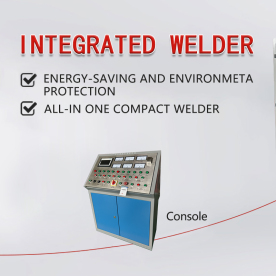
Understanding the Role of an Uncoiler in Modern Manufacturing: Efficiency and Precision in Material Handling and Processing
An uncoiler is a device used to unwind coils of material, ensuring a smooth and consistent feed into production lines. The machinery typically consists of a frame, a spindle for holding the coil, and an unwinding mechanism. When a coil is loaded onto the uncoiler, the device’s drive system gently and steadily rotates the spindle, allowing the material to feed off without causing damage or deformation. The design of an uncoiler varies by application but often includes capabilities for adjusting tension and speed to accommodate different materials and processes.
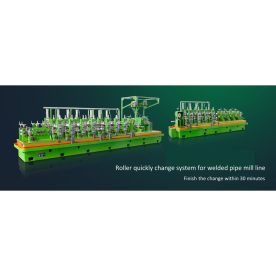
Understanding the Role of an Uncoiler in Modern Manufacturing: Efficiency and Precision in Material Handling and Processing
Importance in Manufacturing Processes
In manufacturing, time is money, and maintaining a streamlined operation is crucial. An uncoiler streamlines the process of moving raw materials into production, reducing labor costs and minimizing downtime. By automating the unwinding process, manufacturers can maintain a continuous flow without relying heavily on manual labor, which can be prone to errors and inconsistencies.
In addition to enhancing efficiency, uncoilers help improve safety in the workplace. Handling heavy coils of material can be hazardous, and employing an uncoiler minimizes the risk of accidents associated with manual handling. The machine is designed to manage the heavy lifting, providing a safer working environment for employees.
Types of Uncoilers
Uncoilers come in various types, tailored to meet specific production needs. The two primary categories are powered and manual uncoilers.
1. **Powered Uncoilers:** These machines utilize electric or hydraulic power to control the unwinding and feeding process. They are suitable for high-volume operations and can handle heavier coils with greater ease. Powered uncoilers often come with advanced features, including digital controls that allow operators to set parameters such as tension and speed for optimal performance.
2. **Manual Uncoilers:** These devices are more straightforward and rely on manual effort to unwind the coils. While they are typically suitable for smaller operations or lighter materials, they do require more labor and can be less efficient in high-demand environments.
Regardless of the type, the choice of an uncoiler should align with the specific requirements of the production line, considering factors such as coil weight, material type, and the desired level of automation.
Integration with Other Machinery
An uncoiler does not operate in isolation; it is often integrated with other machinery in a production line for maximum efficiency. For instance, in metal fabrication, an uncoiler may be used alongside a decoiler, which processes the unwound material into sheets or profiles.
Additionally, uncoilers can be linked to other parts of the inline process, such as feeders, shears, or CNC machines. This integration allows for a seamless workflow that minimizes the need for human intervention, further reducing the risk of errors.
Challenges and Considerations
While uncoilers offer numerous benefits, they are not without their challenges. One consideration is the need for regular maintenance to ensure the longevity and efficiency of the machine. Dust, debris, and wear can affect performance, leading to issues such as material jamming or uneven feeding, which could disrupt the manufacturing process.
Another challenge is the initial investment cost. While uncoilers reduce labor costs and improve efficiency in the long run, procuring and installing the machinery requires considerable capital. Companies must weigh these initial costs against the projected savings and productivity increases.
Conclusion
In summary, the uncoiler is a critical component in modern manufacturing that enhances efficiency, safety, and consistency in material handling. By automating the unwinding process, manufacturers can streamline production lines and reduce labor costs, ultimately leading to a better bottom line. Despite certain challenges, the strategic use of uncoilers can significantly boost operational efficiency, making them an essential investment for any forward-thinking manufacturing operation. As industries continue to evolve, the uncoiler’s role will undeniably remain pivotal in driving innovation and productivity.Solid State HF Welder Replacement Parts