In today’s fast-paced industrial landscape, energy efficiency and advanced material handling techniques are paramount to optimizing production processes. Among the various innovations, vertical accumulators have emerged as a significant solution for enhancing performance across multiple sectors. These innovative devices serve as essential components in logistics, manufacturing, and warehousing, enabling firms to manage their resources more effectively while minimizing waste and improving throughput. In this article, we will delve into the working principles of vertical accumulators, their various applications, advantages, challenges, and the future prospects they hold for industries worldwide.
Understanding Vertical Accumulators
Vertical accumulators are specialized storage units designed to hold a substantial quantity of material, such as pallets, containers, or raw goods, in a vertical orientation. By stacking materials vertically rather than horizontally, companies can maximize floor space in warehouses and production facilities. These accumulators are commonly used in conveyor systems and Automated Storage and Retrieval Systems (AS/RS), where the efficient handling of goods is crucial.
The basic functioning of a vertical accumulator involves a series of belts, rollers, or lifting mechanisms that transport materials to the designated stack. Upon reaching the desired height, the materials can be held in place until they are needed for use. This ability to store materials in a compact format allows businesses to reduce clutter and streamline operations significantly.
Applications Across Industries
Vertical accumulators have found their place across various industries due to their adaptability and efficiency. Some of the key industries leveraging this technology include:
1. **Manufacturing:** In manufacturing plants, vertical accumulators facilitate the smooth transition of parts between different stages of production. By temporarily storing components, manufacturers can ensure that each workstation operates seamlessly without bottlenecks arising from material shortages.
2. **Logistics and Warehousing:** Distribution centers utilize vertical accumulators to manage inventory more effectively. By stacking goods vertically, warehouses can optimize storage capacity and improve order-picking efficiency, leading to faster delivery times and increased customer satisfaction.
3. **Automotive Industry:** In the automotive sector, vertical accumulators are employed to hold components such as tires, engines, or other parts used in assembly lines. Their compact design helps in organizing these components for easy access, thereby enhancing operating efficiency.
4. **Food and Beverage:** In the food processing industry, vertical accumulators play a crucial role in maintaining sanitized environments. They can be used to store raw materials prior to processing, allowing operators to manage stock while adhering to safety regulations.
5. **Pharmaceuticals:** Similar to the food industry, vertical accumulators are vital in the pharmaceutical sector for ensuring the secure storage of sensitive materials. They can help legitimate pharmaceutical manufacturers keep inventory properly organized while complying with health guidelines.
Advantages of Vertical Accumulators
The adoption of vertical accumulators brings several advantages to organizations, including:
– **Space Optimization:** Vertical storage maximizes warehouse height while reducing floor space usage, allowing businesses to accommodate more materials without expanding facilities.
– **Increased Efficiency:** By minimizing the travel distance of materials to and from workstations, vertical accumulators enhance workflow efficiency and productivity.
– **Cost-Effectiveness:** Efficient use of space and improved material handling can lead to significant cost savings in terms of labor and operational expenses.
– **Flexibility:** Vertical accumulators can be tailored based on specific industry needs, sizes, and storage capacities, making them versatile solutions for various applications.
Challenges and Considerations
Despite their numerous advantages, vertical accumulators come with their share of challenges. Maintenance and repair can be more complex than standard horizontal systems due to their vertical orientation and movement mechanisms. Additionally, the initial investment in the technology and training for operators may deter some companies, especially smaller firms with limited budgets.
Moreover, safety concerns must be addressed when implementing vertical storage systems. Proper training and adherence to guidelines are essential to prevent accidents associated with high-stacking and retrieval processes.
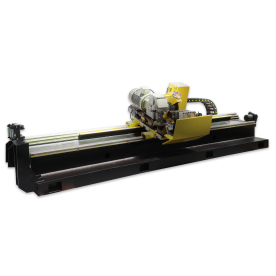
Exploring the Innovations and Applications of Vertical Accumulators in Modern Industrial Systems
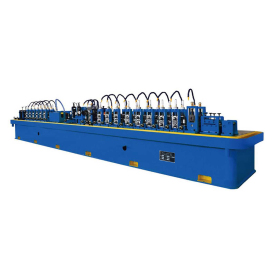
Exploring the Innovations and Applications of Vertical Accumulators in Modern Industrial Systems
Future Prospects
As technology continues to evolve, we can expect vertical accumulators to become even more efficient and integrated into automated systems. With the growth of Industry 4.0 and the Internet of Things (IoT), smarter vertical accumulators will likely emerge, equipped with sensors and real-time data analytics capabilities. This technology could revolutionize inventory management, enabling businesses to anticipate needs and optimize stock levels dynamically.
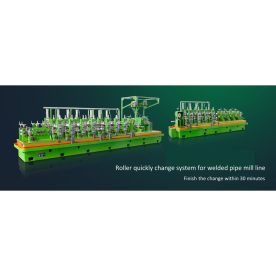
Exploring the Innovations and Applications of Vertical Accumulators in Modern Industrial Systems
In conclusion, vertical accumulators represent a significant advancement in material handling and storage systems, offering businesses across industries a pathway to improved efficiency, reduced costs, and greater flexibility. As industries continue to strive for optimized operations, the adoption of vertical accumulators is likely to see sustained growth in the coming years.Industrial induction heating equipment