In the world of manufacturing, efficiency is key. Every decision made on the production floor can have a ripple effect on the overall productivity of a plant. One piece of equipment that has been gaining popularity in recent years for its ability to streamline processes and increase output is the vertical accumulator.
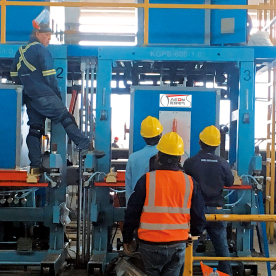
Maximizing Efficiency: The Benefits of Using a Vertical Accumulator in Manufacturing Processes
So, what exactly is a vertical accumulator? Essentially, it is a type of conveyor system that allows products to be stored and accumulated vertically. This means that products can be stored in a much smaller footprint compared to traditional horizontal accumulators. This space-saving design is especially beneficial for manufacturers who are tight on floor space or looking to optimize their layout for maximum efficiency.
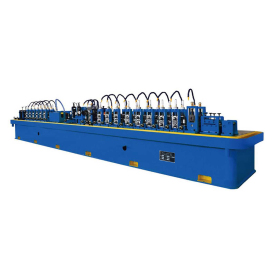
Maximizing Efficiency: The Benefits of Using a Vertical Accumulator in Manufacturing Processes
One of the primary benefits of using a vertical accumulator in manufacturing processes is its ability to improve product flow. By storing products vertically, it allows for a continuous flow of materials and eliminates the need for frequent starts and stops that can slow down production. This results in a smoother and more efficient operation, ultimately leading to increased throughput and decreased cycle times.
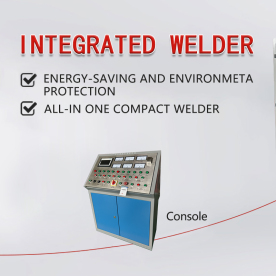
Maximizing Efficiency: The Benefits of Using a Vertical Accumulator in Manufacturing Processes
Furthermore, a vertical accumulator can also help reduce the risk of product damage during handling. Traditional horizontal accumulation systems can cause products to collide or jam, leading to costly downtime and potential damage. With a vertical accumulator, products are gently stored and released in a controlled manner, minimizing the risk of mishaps and ensuring product integrity.
Another key benefit of using a vertical accumulator is its flexibility. Manufacturers can easily adjust the system to accommodate different product sizes and shapes, making it ideal for a wide range of industries. Whether you are producing smaller items like electronics components or larger items like automotive parts, a vertical accumulator can be customized to meet your specific needs.
Additionally, vertical accumulators are known for their reliability and low maintenance requirements. With fewer moving parts compared to traditional accumulation systems, there is less risk of breakdowns and downtime. This means that manufacturers can focus on their core operations without having to worry about constant repairs and maintenance.
In conclusion, the use of a vertical accumulator in manufacturing processes can offer a wide range of benefits, including improved product flow, reduced risk of damage, flexibility, reliability, and low maintenance requirements. By investing in this innovative technology, manufacturers can maximize efficiency and productivity on their production floor, ultimately leading to a more streamlined and profitable operation.Scalable Pipe mill production line system