Vertical accumulators are essential components in modern hydraulic and pneumatic systems, providing critical energy storage and pressure stabilization functions. As engineering and technology advance, the demand for efficient, reliable, and compact energy storage solutions has increased significantly. Vertical accumulators have risen to prominence due to their unique design characteristics and operational capabilities, making them indispensable in various industrial applications.
At their core, vertical accumulators operate on a simple principle: they store hydraulic energy in the form of pressurized fluid within a cylindrical vessel. The vertical orientation of these accumulators allows for optimal space utilization, especially in environments where floor space is at a premium. This design not only ensures efficient fluid flow but also facilitates the easy integration of the accumulator into pre-existing systems without the need for extensive modifications.
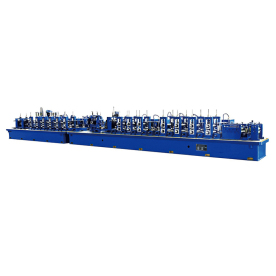
Understanding the Functionality and Applications of Vertical Accumulators in Modern Fluid Power Systems
The functionality of a vertical accumulator is primarily based on its ability to store energy during periods of low demand and release it when required. When a hydraulic system operates, pumps circulate fluid under pressure. When there is an excess of pressure, the fluid is directed to the accumulator, where it is stored under pressure. In times of high demand, the accumulator releases this stored energy, providing an additional flow of fluid to the system and maintaining consistent pressure levels.
One of the noteworthy advantages of vertical accumulators is their ability to minimize pressure fluctuations within hydraulic systems. In many industrial processes, maintaining steady fluid pressure is crucial for ensuring smooth operation and preventing damage to machinery and equipment. The accumulator acts as a buffer, absorbing peaks in pressure and releasing fluid during drops, thus stabilizing the system and improving overall efficiency.
Vertical accumulators come in various designs, with the most common being bladder-type and piston-type accumulators. Bladder-type accumulators consist of a flexible bladder that separates the hydraulic fluid from a gas, typically nitrogen. This configuration allows the bladder to expand and contract, accommodating changes in fluid volume while maintaining pressure. On the other hand, piston-type accumulators utilize a piston to separate fluid and gas, which allows them to handle larger volumes of fluid compared to bladder types.
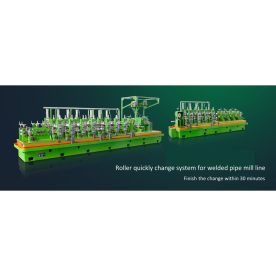
Understanding the Functionality and Applications of Vertical Accumulators in Modern Fluid Power Systems
The applications of vertical accumulators are extensive across multiple industries. In the manufacturing sector, they are used in hydraulic presses, injection molding machines, and other equipment where consistent pressure is crucial for operations. In the automotive industry, vertical accumulators are often integrated into braking systems to provide quick responses and reliable performance. Additionally, they play a significant role in construction equipment, such as excavators and cranes, where they help manage the hydraulic systems amid variable load conditions.

Understanding the Functionality and Applications of Vertical Accumulators in Modern Fluid Power Systems
In the energy sector, vertical accumulators are increasingly employed in renewable energy systems, such as wind and solar power plants. They assist in storing excess energy generated during peak production times and releasing it during periods of high demand or low generation. This capability significantly enhances the reliability and efficiency of renewable energy systems, contributing to the transition toward more sustainable energy solutions.
The integration of vertical accumulators in modern hydraulic systems also aligns with advancements in smart technology and automation. With the rise of Industry 4.0, these accumulators can be monitored and controlled remotely, allowing for real-time adjustments and improved operational efficiency. Sensors can provide critical data on pressure levels, fluid volume, and overall system performance, enabling predictive maintenance and reducing downtime.
However, while vertical accumulators offer numerous benefits, it is essential to understand their limitations and ensure proper maintenance. Over time, the bladder or piston within the accumulator may wear, leading to reduced performance. Regular inspection and maintenance protocols are necessary to ensure that the accumulator operates at optimal efficiency and reliability.
In conclusion, vertical accumulators are vital components in fluid power systems, providing energy storage, pressure stabilization, and operational efficiency. Their unique design, coupled with a broad range of applications across various industries, makes them an indispensable element in modern engineering. As technology continues to evolve, the role of vertical accumulators is poised to expand, offering innovative solutions that meet the ever-growing demands of industrial applications. Proper understanding and maintenance are critical to maximizing their performance, ensuring they remain at the forefront of fluid power technology.High-efficiency All-in-one Welding System